Automation of logistic processes at meat processing plant Atyashevsky with SAP based solutions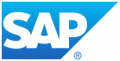
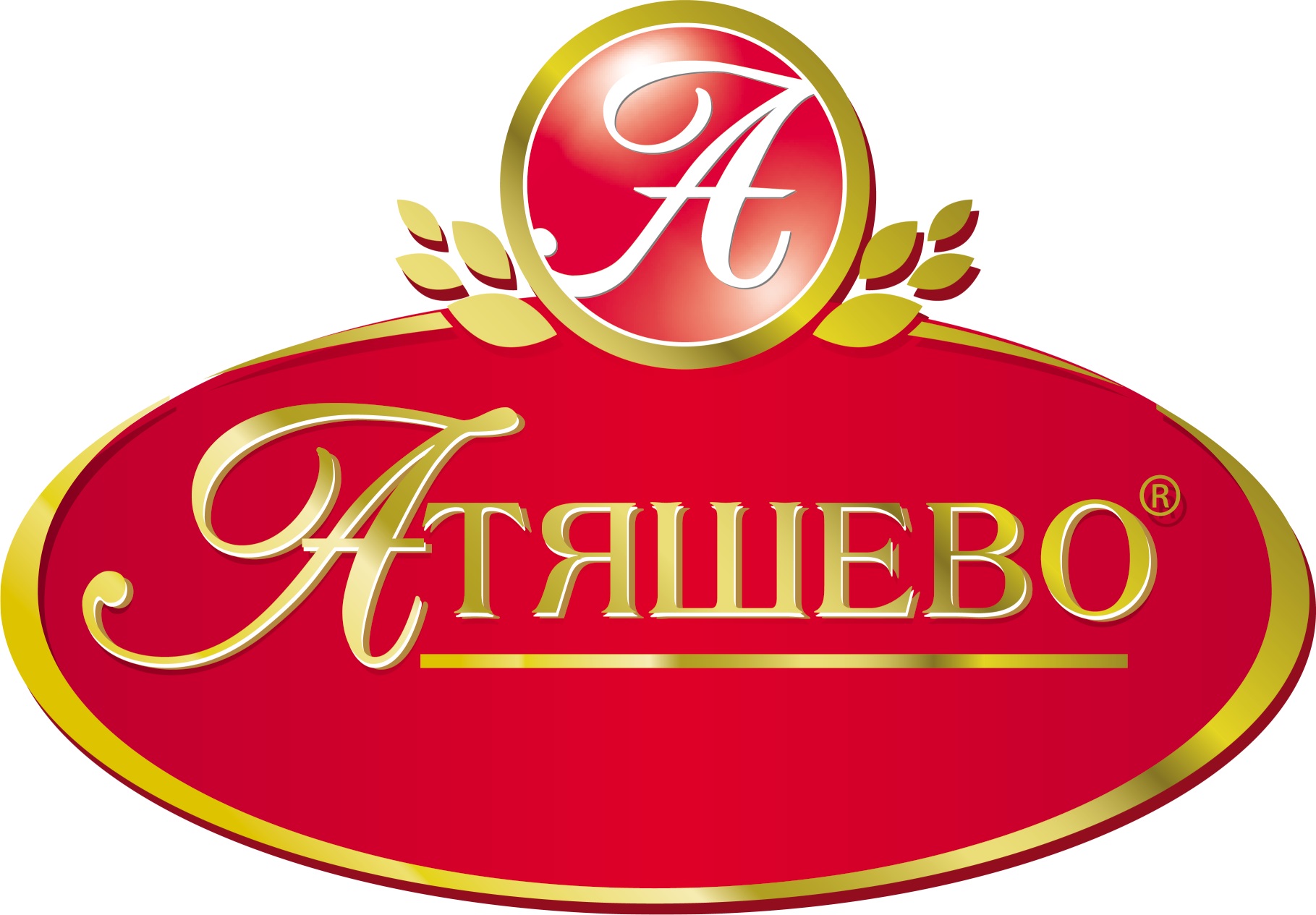
Statement of the problem and requirements to WMS
- The system must have addressed storage principle,
including the using of gravitational racks.
- There should be implemented the possibility of production and execution of warehouse tasks in two parallel units: kg and boxes.
- The system should automatically receive and putaway processing units (EO) for customized strategies for different types of racks.
- The system should be easily administrated.
- Online monitoring of all processes. Required analytics. Warehouse resource management warehouse in real time.
- Seamless integration of WMS wiith accounting systems (1C: Manufacturing, 1C: Trade, 1C: Accounting).
- Personalization of warehouse processes.
- The scalability of the system in case of expanding of company’s business.
PRODUCT CATEGORIES
- Calibrated sausage products, which do not
require additional packaging in boxes.
- Weight production, measured both in kilograms and boxes (each box has a unique weight).
QUANTITATIVE EVALUATION
- The area of the warehouse class A — 4 200 sq.m.
- Topology:
— Racks
— Flow racks - SKU – about 150
- Picking lines during a working shift – not less than 15000
- Working mode — non-stop
- Temperature mode — +2…+6 °C
General processes
- Acceptance of final goods (FG) from automated in-line and discrete product lines, and also from vacuum packaging shop.
- Quantitative and qualitative account of FG with tracking of production date,
shelf life, production batches and attachment to the customer at the consignment level.
- The address storage of FG in compliance with the climatic conditions and the turnover.
- Timely preparation and shipping of goods (box / pallet) to recipients.
- Dynamic replenishment of box-picking cells with necessary quantity of products for an order.
- Internal movements, inventory, repackaging.
- Integrated weight control at the entrance and exit from the warehouse.
- Supporting of warehouse turnover with required printed documentation.
- Support of warehouse processes with analytical reporting.
- Throughout online monitoring of all warehouse movements.
Decision of TLS
|
|
In the first phase of the project the automation of warehouse processes for acceptance of calibrated and weight-production, placing it on a rack storage areas of various types, distribution and shipment for client orders has been implemented. Besides, processes of inventory, weight control, processing of returns to manufacture, rejection and internal auxiliary movements have been realized.
FOLLOWING POSITIVE RESULTS HAVE BEEN ACHIEVED: 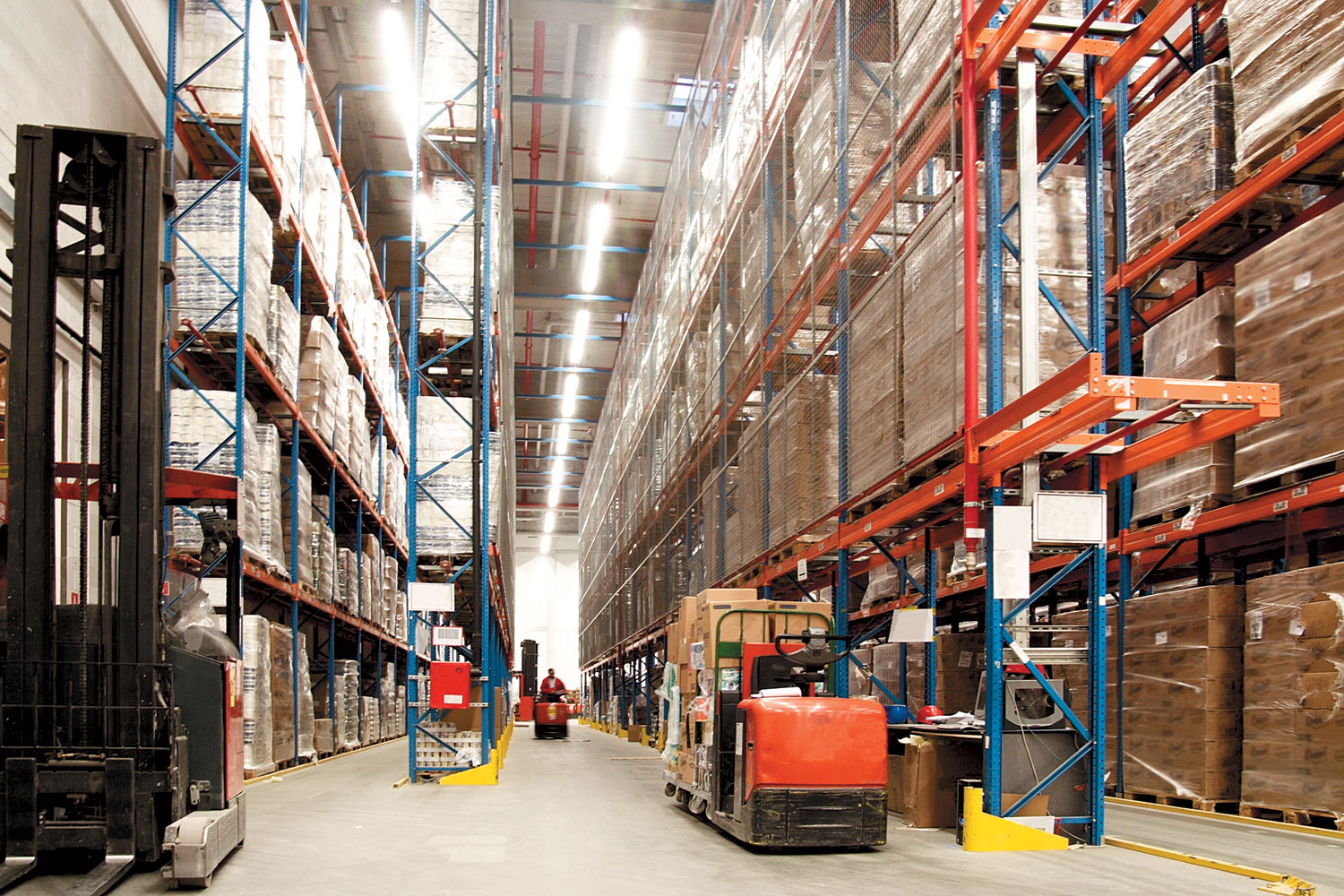
- The percentage of errors in quantity of products at orders picking has been reduced.
- Flexibility and transparency in organization and management of intra-movement of stocks have been increased.
- Speed and accuracy of picking and the accuracy of inventory reporting on warehouse stock have been significantly improved.
- Accuracy of production planning and shipments to customers have been increased.
- Working of resources in the warehouse has been optimized by implementing of tool Working under control of the system.
- Control of shipment gates and transport units in Yard Management module allowed to significantly increase the speed and accuracy of the loading and release of materials.